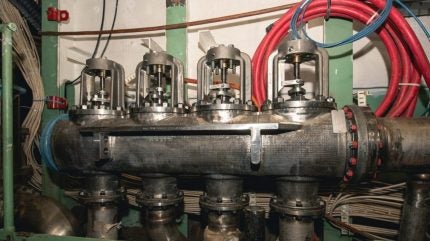
Huntington Ingalls Industries’ (HII) Newport News Shipbuilding division has installed the first 3D-printed valve manifold assembly on Gerald R. Ford-class aircraft carrier, Enterprise (CVN 80).
The integration of additive manufacturing, or 3D-printing, into shipbuilding is poised to enhance the speed and quality of construction for critical components, potentially shortening lead times and accelerating the delivery of vessels to the US Navy.
The valve manifold assembly, required for distributing fluid from a single source to multiple points on the ship, is situated in a pump room of the aircraft carrier.
Measuring approximately 5ft in length and weighing 1,000lb, the assembly was produced in collaboration with DM3D Technology.
This advancement in additive manufacturing follows HII’s prior certification as a supplier for 3D-printed components on Naval Sea Systems (NAVSEA) platforms.
the company said that similar manifold assemblies for the Doris Miller (CVN 81) are set to be created using additive manufacturing techniques instead of traditional casting methods.
This shift is expected to mitigate schedule risks and enhance overall efficiency in the shipbuilding process.
NNS Enterprise (CVN 80), Doris Miller (CVN 81) and future aircraft carrier programmes vice president Les Smith said: “It is only fitting for this Enterprise, CVN 80, to be part of a historic first at NNS, considering the previous Enterprise, CVN 65, was the world’s first nuclear-powered aircraft carrier, proudly built here at the shipyard.
“Thousands of dedicated shipbuilders are working with urgency on these aircraft carriers that we know will play a vital role in the Navy’s fleet.”
In 2022, HII ceremonially initiated the construction of the USS Enterprise, the third Gerald R Ford-class aircraft carrier for the US Navy.
in 2024, HII announced the successful transfer of the mid-body hull section of the Enterprise (CVN 80), enabling the concurrent assembly of two Gerald R. Ford-class aircraft carriers in the same dry dock.
To date, more than 55 additively manufactured parts have been installed on both new and existing fleet vessels, with plans to integrate more than 200 additional parts within the year.