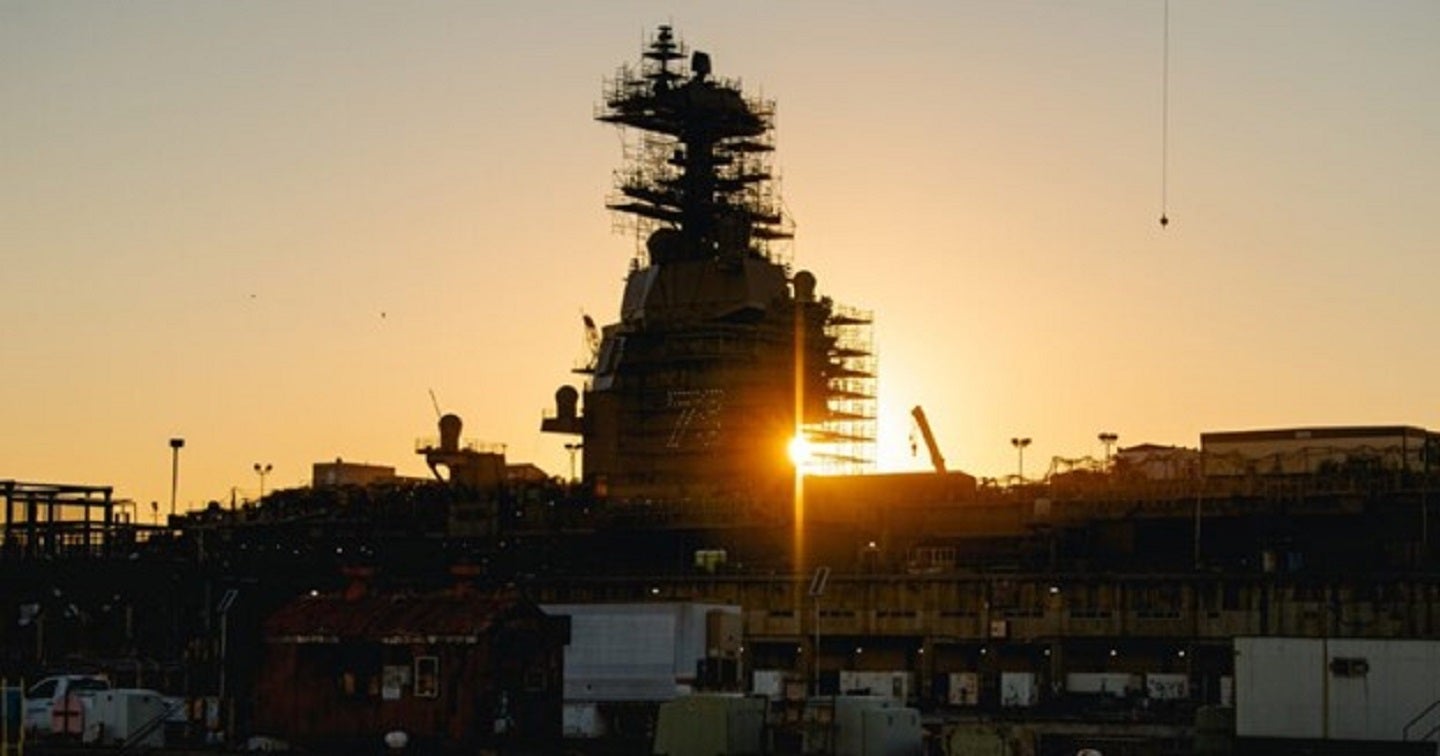
Shipbuilding has always been a famously lengthy development process, and the new demands across defence for contractors to balance time and capability to an optimal level will only strain schedules even further.
However, thanks to developments in advanced manufacturing methods such as 3D printing, the American naval manufacturer HII claims these tech developments will “save thousands of man-hours over time.”
An engineer at HII’s Newport News Shipbuilding division has designed an upgraded spot face cutting tool using 3D printing, which was needed to work aboard John F. Kennedy (CVN 79), a US Navy Gerald R. Ford-class aircraft carrier.
Overcoming shipbuilding delays and cost growth
While this may appear to be a small success on the surface, it actually represents the future potential to cut down shipbuilding timeframes at a time of intensifying military demand as our geopolitical environment sours. Particularly in the Indo-Pacific where the US-China rivalry will increase naval production.
The US Government Accountability Office (GAO) has often tackled the problem of cutting down shipbuilding delays for the US Navy. Recently, the government agency noted that the navy “experiences years of construction delays, billions of dollars in cost growth and frequent quality and performance shortfalls,” which leads to it accepting delivery of incomplete ships after significant delays.
3D printing solutions
The conventional manufacturing route would have taken weeks but meeting schedule requirements for the CVN 79 required a faster, more efficient approach without sacrificing quality.
“This tool example demonstrates the benefit of long-term strategic thinking,” Deputy Chief Engineer John Ralls said. “Newport News Shipbuilding has taken a leadership role in specific technologies, additive manufacturing being one of them. We have removed numerous roadblocks that have enabled us to support emergent parts like this spot face cutting tool.”
HII uses carbide inserts that can be rotated or replaced. Whereas the old cutter is made from steel and must be sharpened almost daily. This adds another level of efficiency in rendering the tool an adaptable and versatile piece of manufacturing equipment.
By 2030, 3D printing, or additive manufacturing, will be a $70.8bn industry, having grown at a compound annual growth rate of 18% between 2021 and 2030, according to GlobalData forecasts.