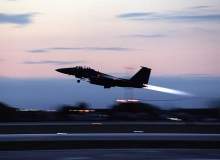
At peak thrust, an F-15 ignites 25 gallons of fuel a minute, while a heavyweight B-52 bomber easily consumes double that – around 50 gallons a minute, equating to about 86 barrels an hour.
As a result, the United States Air Force (USAF) single-handedly accounts for 64% of the Pentagon’s entire fuel bill and more than four fifths of it is used in the air, with the USAF spending some $6.7bn on aviation fuel in 2010 alone.
It all adds up to a huge slice of the defence budget and it is a picture which is broadly repeated around the world. With cuts widespread and fuel costs escalating, it comes as little surprise that the search is on for innovative ways to cut consumption.
Cutting costs
One self-evident way of making an instant reduction is simply to fly less, and it is an approach that a number of air forces are actively exploring by making additional use of flight simulators to help cut some of the high fuel costs of training. According to the recent ‘From Barracks to the Battlefield’ Pew Project on National Security, Energy and Climate report, increasing the role of simulation should represent a saving of as much as $368 million to the USAF in the fiscal year 2012, and the run-on benefits could be even greater.
The report also highlights other initiatives, including continued R&D work on the highly efficient embedded turbine engine (HEETE) and the adaptive versatile engine technology (ADVENT) programme, along with targets to reduce the fuel burnt in existing US aircraft by 5% by 2016, 10% by 2020 and 20% by 2030.
In addition, a range of other strategies – to provide fuel-efficient routing, improve centre-of-gravity optimisation, manage crew ratios and avoid over-fuelling – are also expected to save around $59m by 2012.
However, it is the production of biofuels that arguably offers one of the most potentially effective avenues to achieve the necessary cost cutting required in the long-term.
The appeal of biofuels
The idea of manufacturing alternative fuels capable of acting as direct substitutes for their conventional counterparts is nothing new. Both the automotive and aviation industries have courted the prospect for decades, with products derived from a wide range of organic wastes, energy-crops and other similar materials, but development has often been hampered by questions of land usage and the inherent difficulties in producing on a scale large enough to be economically competitive.
Now, however, with the USAF intent on flying on domestically produced alternative fuels by 2030, and an interim goal set to meet half its annual demand for domestic aviation – around 400 million gallons – by 2016, biofuel production seems to have been presented with a real incentive.
It is something of a challenge too. As the programme to certify their fleet to run on a 50:50 blend continues to gather momentum, USAF deputy assistant secretary for energy, environment, safety and occupational health Timothy Bridges recently likened it to a gauntlet thrown down to the industry.
To date, the service has principally approved fuels produced by the Fischer-Tropsch process, a method which turns carbon-rich materials, such as coal or natural gas, into a liquid fuel known as synthetic paraffinic kerosene.
However, with new biofuels – such as the plant oil derivative, hydro-treated renewable jet (HRJ) – being constantly developed and improved, the Air Force Research Laboratory is busily testing and certifying as many of them as possible, following what has been described as a ‘feedstock and process-agnostic’ approach. The only proviso is they must function in a way that is indistinguishable from conventional JP-8 aviation fuel.
Algae and aviation
Part of the drive behind developing such biofuels lies in the US’ desire to break its current dependency on foreign oil, which represents an obvious potential weakness and makes manufacturing fuel sustainably, from readily available domestic sources, a highly desirable capability.
Although opponents of biofuel production have often criticised the idea of energy-cropping on the grounds of its frequent competition with agricultural crops for prime growing land, there are some feedstocks – ideal because of their high plant oil content – which can be successfully cultivated with little or no detriment to food production.
Camelina – otherwise known as false flax – is one which has found particular favour, largely because it can be grown on wheat fields during their fallow period, thus avoiding the need to permanently displace food crops, but it is the potential of algae that seems to be getting the most attention.
There has been a lot of hype regarding the promise of algal biofuels, and some of the estimates of their supposedly unbridled productivity peddled over the years have been, quite frankly, ludicrous.
Nonetheless, while the yield of oil from even the best land plants rarely exceeds 500 gallons an acre, Nasa’s work on the pyramidal micro-alga Botryococcus braunii under the umbrella of the ‘Spaceship Earth project’ suggests that more than 1,500 gallons/acre really is a practical possibility. It is something which the US Defense Advanced Research Projects Agency (DARPA) is taking very seriously.
A dollar a gallon
DARPA research projects, undertaken by private companies SAIC and General Atomics, are already reported to have shown the way to produce oil from algae at projected cost of around $2 per gallon, with an eventual goal of cutting that in half once the technology matures and economies of scale kick in.
Oil at a dollar a gallon – and refined jet fuel at $3 or less – would make biofuels directly competitive with conventional petroleum products, and that would be a real game-changer.
It seems a large-scale refining plant capable of producing 50 million gallons of this new, revolutionary jet fuel is just around the corner. According to DARPA, production is scheduled to begin in earnest in 2013, with algae providing the oil feedstock, at an expected yield of 1,000 gallons an acre.
If initiatives such as this do ultimately see low cost alternative fuels become a reality, the implications will be enormous, not only for the world’s air forces, but for the whole of the aviation industry too. In June 2011, a Gulfstream G450 powered by Honeywell Green Jet Fuel made the first ever biofuel transatlantic flight. The way things are going, it is unlikely to be the last.