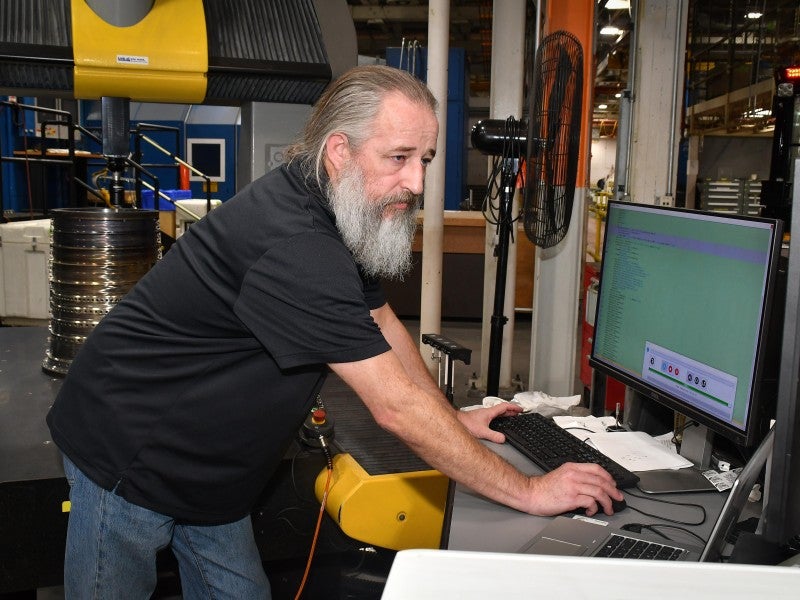
US Fleet Readiness Center East (FRCE) has successfully completed a process improvement project to boost the production and depot ability to deliver aircraft and its components.
The FRCE Repair Machine Shop comprises of a total of 22 work centres that support and recondition components and parts of a wide range of military helicopter and aircraft. It employs around 70 highly trained machinists.
The refurbishment of some components of older aircraft is necessary, as they are no longer in production.
As part of the new process, the shop’s supervisors and machinists used different data visualisation tools to consolidate information from different databases in one place.
The new home-grown module, referred as Enhanced Production System (EPS), further minimised the turnaround time of repairing the components from 17 days to five.
FRCE Machine, Paint and Clean Branch head Matt Sinsel said: “Now, we’re putting more quality parts on the shelf faster.”
According to FRCE Industrial Process and Engines director Don Jeter, every component repaired at the shop requires different level of work, depending on the different climatic and regional conditions the aircraft operates in.
Jeter added: “You can have six identical housings come in with each needing drastically different repairs.”
In order to divide work on the basis of priority levels, the FRCE team implemented a data analytics platform, called Qlik Sense. It helped the team to create reports that interpret detail and status of in-process components.
Repair Machine Shop machinist Robert Hampson said: “It allows you to plan ahead and avoid backlogs. We can also cross-train a little bit more this way.”
The team at Repair Machine Shop has now started working on the next phase of the process improvements to reduce the average number of days to three.