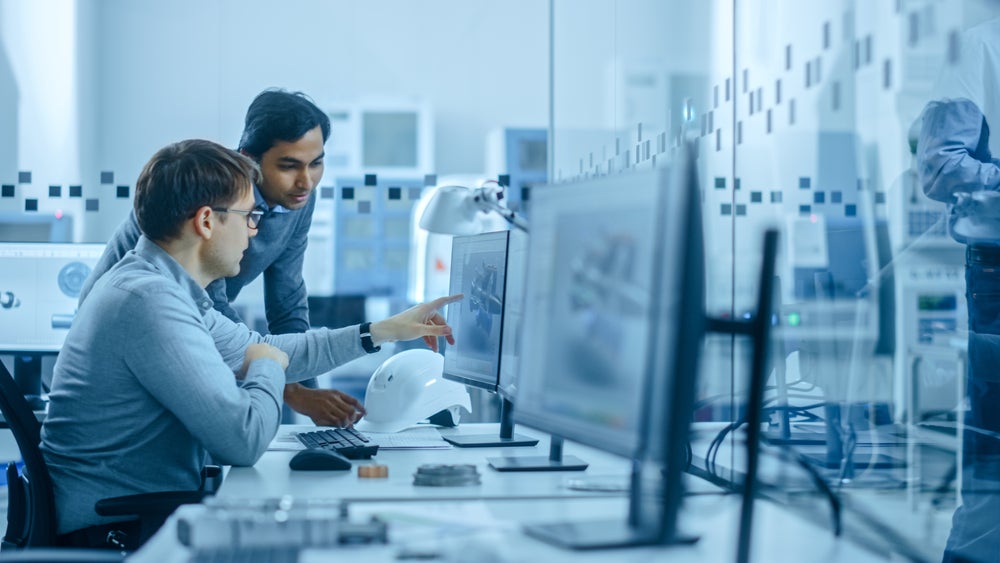
The shipping industry is on the precipice of major change. There are ESG (environment, social and governance) pressures: the International Maritime Organisation (IMT) has mandated 50% reductions in shipping emissions by 2040. There is pressure to innovate: integrating next-generation materials and fuels into existing vessels is a daunting task. And gaining a competitive edge could mean ballooning costs as shipyards chase finer and finer margins in the race to stay ahead.
Traditional ship design consists of four phases: concept, preliminary, contract and detail. These phases are governed by their own “spiral” of requirements, including powering, arrangements, stability and costing. But technological and regulatory change is overwhelming the ability of this long-established process to get from design to finished vessel quickly and efficiently. More data needs to be processed, more supply chain stakeholders must be accommodated, and more collaboration is needed between increasingly siloed teams.
Marrying up disparate teams and data streams necessitates an alternative approach. One solution is to orchestrate better processes, enabling oversight, management and automation of workflow between siloed teams – even when they are using different systems and working to different timelines. Orchestrating processes via product lifecycle management (PLM) software provides experts with reassurance that everyone working on a project is speaking the same language, saving time that would otherwise have been spent trying to surmount communications barriers and negotiate evolving requirements.
A suite of new tools and software is entering the market to aid these tasks. But before examining these solutions, it is essential to understand the problems they are addressing – and why addressing them now is vital.
Pressure 1: Environment
Rhetoric around the climate crisis has been ramping up over recent years. At COP26 in 2021, banks, insurers and investors promised $130 trillion of private capital to fund the energy transition. A year later, at COP27, the Sharm el Sheikh implementation plan suggested $6 trillion could be needed to hit global net zero targets.
GlobalData estimates suggest rhetoric is starting to translate into action. The shipping industry will need to keep pace.
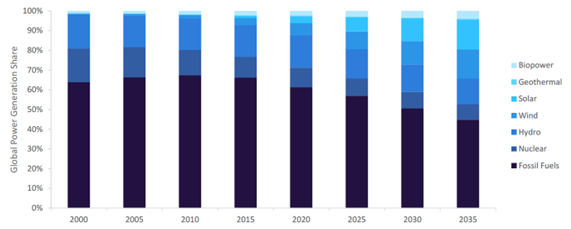
Reliance on oil, coal and gas in global power generation is expected to drop precipitously in the runup to 2035. Initiatives designed to remove carbon from the atmosphere – as well as stop it getting there in the first place – are also on the rise, with GlobalData projections pointing to a nearly fivefold increase in carbon capture capacity between 2023 and 2030.
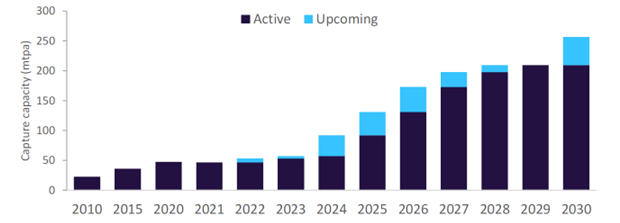
Two implications stand out for ship designers. First, supply chains will have to be rethought. ESG imperatives mean that high-emission sectors central to shipbuilding – like steel – will be under intense scrutiny, forcing naval architects to become much more discriminating about the partners they work with. Second, rising popularity and crashing costs of carbon capture will make production of blue hydrogen – hydrogen manufactured using natural gas, the emissions of which are stored underground to create an environmentally friendly fuel source – increasingly viable. This could turbocharge its use in zero-emission batteries that will become commonplace in next-generation vessels (more on that below).
Pressure 2: Innovation
Amid the environmental imperatives, green innovations are permeating once carbon-intensive industries. But adapting to these innovations – particularly in the conservative world of naval architecture – represents a challenge.
In the short-term, liquid natural gas (LNG) offers a convenient, lower carbon alternative for diesel-fuelled ships. In the medium term, fuels like methanol and ammonia should enable shipyards to shrink their vessels’ carbon footprints still further. Leading oil giants BP and Chevron are investing heavily in biorefineries, with both planning to produce 100 million barrels per day (mbd) of biofuels each by 2030. Although cheap and less damaging from a global warming standpoint, such fuels still produce emissions that can be toxic for human and animal life. In the long-run, alternative fuel producers are expected to turn their attention to low-cost, low emission hydrogen.
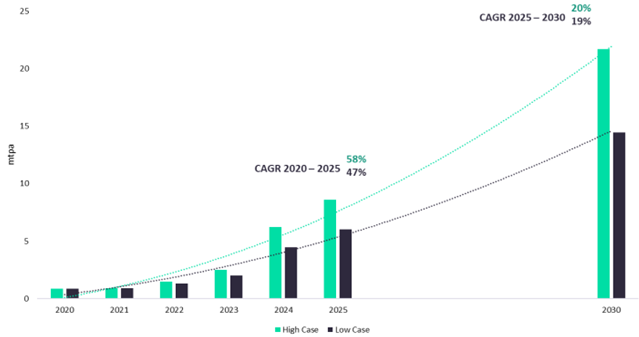
Using data on planned pipeline constructions, a high-end scenario suggests 22 million tonnes of hydrogen could be produced every year by 2030. This would put the compound annual growth rate (CAGR) of hydrogen capacity at a whopping 58% between 2020 and 2025, and another 20% between 2025 and 2030. This includes blue hydrogen, but also green hydrogen – manufactured via renewable-powered electrolysis of water molecules, weaning heavy industry off fossil fuel reliance altogether. Policymakers are leaning into change; the European Union has announced green hydrogen capacity will rise to 80 GW by 2030, while Japan and South Korea both plan to increase their green hydrogen capacities to 15 GW by 2040. Despite issues around storage – its low density means it must be kept in either incredibly low temperature or high-pressure environments to stop it dissipating – a battery-powered revolution is underway, and hydrogen’s abundance and cleanliness make it a safe bet for a fuel of the future.
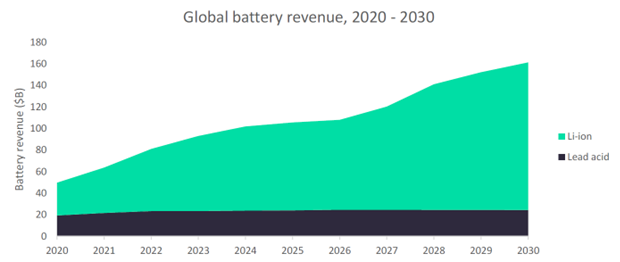
GlobalData forecasts battery industry revenues of over $168 billion by 2030 compared to $55 billion in 2020, equivalent to a 14% CAGR over the period. Revenues from lead-acid batteries will see only incremental growth, whereas sales from Li-ion batteries will drive much of the expansion, occupying an increasing percentage share of the total batteries market. As hydrogen capacity increases, so too will its role in fuel cells for use in the transportation industry. More innovation will be needed to make it viable in shipping – the low power-density ratio of batteries makes them unsuitable for long-haul voyages – but the rise of hydrogen and other alternative fuels will force naval architects to overhaul propulsion systems and the processes governing their design.
Pressure 3: Competition
Shipyards know they must make their vessels more environmentally friendly, and that incorporating efficiency gains on offer from the latest innovations offers a route for doing so. But industry data suggests costs associated with creating next-generation fleets is stalling progress. By the end of November 2019, the global vessel order book had fallen to 2,952 vessels of 1000 gross tonnes or more in size, totalling just over 74 million compensated gross tonnage (CGT). This represents a 14% decline in 2019 in CGT terms – and a decline of 67% from the 2008 peak in global orders.
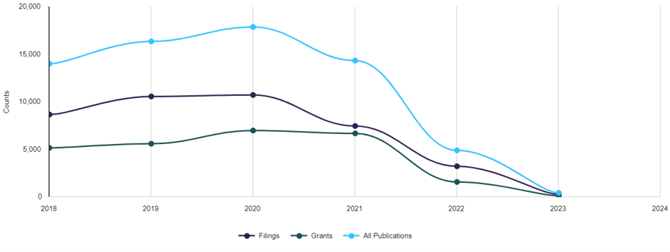
Similarly, analysis of GlobalData’s patent database points to a sharp drop in the total number of filings right across the transport industry since 2020. Amid rising prices, frail supply chains and geopolitical instability, shipyards are anxious about their ability to compete as the industry evolves – and are retrenching as a result.
Confronted with stringent ESG mandates, progress towards meeting the ambitious goals laid out by the IMT is at risk of plateauing. The solution is for naval architects to deploy processes that allow them to meet evolving design briefs, incorporate new technologies without compromising cost ceilings and ultimately compete in a changing industry.
Get to grips with data via process orchestration
Adaptability and flexibility are needed throughout the design process to account for changing needs across a ship’s lifetime. Rather than burying their heads in the sand over the complexity this creates, ship designers should embrace it. Adopting a PLM system tailored to the marine industry can help make this possible. This is exactly what Teamcenter offers, serving as a centralised source of data on projects where competing requirements would otherwise slow the race to fulfil a brief. Teamcenter enables data from before, during and after a vessel’s launch to be modelled in one central environment. The data is built into an ongoing design process, ensuring requirements for different teams are harmonised as part of a ship build.
Consider a pump in a ship’s piping system. It could play a role across multiple systems, each with specific requirements and governed by different teams. Using Teamcenter allows links between these requirements to be meticulously traced; a complete picture of the pump’s needs can thus be created without duplicating information or compromising quality. This traceability enables the thread of design requirements to run smoothly through the design and simulation process.
“What-if” tests are another key feature of a data-rich PLM system. These can assess design configurations in a virtual environment during decision making processes about where to place heavier batteries, how to accommodate lighter hulls and the best ways to cut down on energy consumption. To do so requires processing of massive amounts of data – but the model-based engineering process puts all the power in the hands of the end user. Users can easily find the information they need and have an engineering change notification system on hand to reveal where consequential changes have been made by other users too.
As the next generation of shipping arrives, mastery over data streams will be crucial for maximising efficiency. The solutions on offer from Siemens Digital Industries Software simplifies the sprawling design process, making designers more productive. By embracing complexity and implementing orchestration, shipbuilders have all the data they need on requirements and specifications at their fingertips. Download the whitepaper on this page to find out more about the next generation of naval architecture and how you can start using PLM to orchestrate better processes.