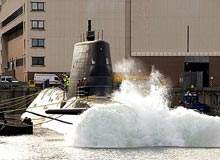
BAE Systems’ new Astute submarine is simply awesome.
A more complex engineering project than a space shuttle, the 97m-long Astute is made up of more than one million components and was built with the aid of more than 7,000 design drawings.
The submarine, capable of circumnavigating the globe without surfacing, contains such advanced nuclear technology that it will never have to be refuelled. And its advanced weapons systems mean it can land a Tomahawk cruise missile on a sixpence from 1,000 miles away.
The importance of Astute runs deeper than the 150m the submarine is capable of diving to. BAE Systems was initially contracted to build three Astute Class submarines (Astute, Ambush and Artful) for a total cost of £3.5bn.
The success of Astute has prompted the Ministry of Defence (MoD) to signify its intention to order seven Astute Class submarines in total. They’ve already commissioned a fourth submarine, Audacious, which will see another £200m flood the BAE coffers.
It’s all good news for BAE’s 3,500 staff in Barrow, plus the estimated 2,400 other people in the UK who are employed as a direct result of the Astute project. Business is booming, Barrow is thriving and the future looks bright. But it was all nearly so very different.
In 2003 the Astute project was £900m over budget and running four years late. The MoD was not going to give BAE another contract to build a surface ship and the future of Barrow looked very bleak. Then Murray Easton, BAE Systems Submarine Solutions’ tenth managing director in as many years, arrived and things started to change.
Paul French caught up with Murray to find out how he managed to turn the Astute project around, what it means for Barrow and how it positions BAE in terms of the new Trident platform.
PF: What was morale like when you arrived?
ME: Morale was very poor indeed both internally and within the Ministry of Defence.
PF: How had things become so bad on the Astute project?
ME: I don’t think the demands of building a submarine had been fully comprehended. You have to utilise every spare millimetre of space, so the demands are extreme. It was the first time they’d used a 3D model on CAD at Barrow. Systems were not developed and it caused a lot of problems.
The other major problem was the fixed-price contract that GEC (which had the contract before BAE Systems) had with the MoD.
This was a first of class and submarines aren’t like tanks, where you build a prototype and iron out the kinks that way. Our first of class had to end up in the water.
The entire authority for the design, the build, everything rested with GEC. There was huge capability within the MoD but there wasn’t sufficient access to that. GEC underestimated what it would take. Once they got the contract, they realised it was too big an elephant to chew.
When the contract migrated to BAE Systems (after they acquired GEC in 1999) it perpetuated the problem. I joined BAE in June 2002 but by December I’d had enough and I left. Then in March 2003 I came back in my current capacity and we re-baselined the programme.
PF: How did you use technology to turn things around?
ME: Astute is one of the first nuclear submarines to be designed entirely in a three-dimensional computer-aided environment. It breaks away from the principle that submarine performance should be optimised by designing the smallest boat possible with little regard to cost.
The programme relies heavily on the power of computer-aided design and ‘virtual prototyping’ because with a project as complex as Astute there is no time or budget to produce an actual prototype submarine.
Instead, ‘virtual’ prototyping is relied upon, harnessing the power of computer test and visualisation, along with continuous design and systems analysis.
Over one million components are represented on the three-dimensional CAD model, which together with analysis and integration rigs, represents the completed vessel. Three-dimensional CAD also enables the exchange of critical design data across the supply chain, and allows change to be implemented efficiently and effectively.
PF: What about modular building?
ME: The adoption of a modular build strategy has played a crucial role in achieving the current accelerating production schedule for the Astute submarine project, and BAE Systems Submarine Solutions is seeking to increase the modularisation in successive Astute Class builds.
Recognition of the unique challenges of commissioning a first-of-class submarine has driven high achievement in the build and integration stages. Since 2004 every module has been shipped on, or ahead of, schedule.
PF: And vertical outfitting?
ME: Vertical outfitting was actually first introduced on the second Astute Class vessel – Ambush – and is a technique that was adopted from its success with Electric Boat in the US. Since then it has been refined and is used for virtually every hull section.
Vertical outfitting involves the circular sections of the submarine being turned to stand ‘on end’ in a vertical configuration as opposed to the traditional method of building in a ship-wise or horizontal configuration.
It enables large, heavy or unwieldy equipment to be shipped in and offers huge advantages in terms of efficiency, thousands of man hours saved, and health and safety gains.
In addition, a flexible staging system enables the outfit teams to work on a 360º face at shoulder height, as opposed to working in the horizontal mode when work faces could be at the fitter’s feet or above his head. Again there are massive efficiency and health and safety gains.
PF: What measures did you use in terms of dealing with the staff?
ME: When I arrived there was a divisive PCO (prime contract office) structure, which meant the PCO was effectively the internal customer, whilst the marine side of the business was responsible for the design, build and delivery of the submarine.
Also, the focus of senior management was in Farnborough, rather than Barrow where the majority of the workers are. When the heat of the fire was on, we needed key staff there to put it out.
I approached the government and was given the green light to collapse the PCO structure. I banned words like marine and PCO and created a one-team approach. We spent a lot of time and money on building teamwork in the company.
After a year I noticed there were still a lot of behavioural issues within the team. People were antagonistic towards each other and not collaborative so we got some psychologists involved who devised different mechanisms for working together.
They’d travel around the factory interviewing staff in confidence and people really opened up to that. Then they’d come to board meetings and suggest ways we could work together better.
We also devised a bonus scheme that was performance-driven. It’s not a handout but everyone in the team, from the fitters to the tea ladies, gets the same, as long as they meet their targets.
In January 2006 we had a pop concert onsite to say thank you to the staff. Heather Small from M People sang to the 6,000-strong crowd, made up entirely of BAE staff and their partners. It was fantastic as the workers could show their partners the submarines and take a real pride in what they’d done.
PF: How have you made use of different engineers on the project?
ME: We’ve used nuclear engineers to provide safety and performance improvements to a state-of-the-art pressured water reactor that is fuelled for life.
Systems engineers have integrated the thousands of sub-systems that require up to 100km of cabling, 23,000 pipes and over five million lines of software code – all whilst managing the supply chain, which consists of more than 30 main suppliers.
Marine and mechanical engineers have provided solutions for the propulsive power train, auxiliary systems and life support. Astute must be quiet, vibration free and robust enough to withstand a nearby underwater explosion.
Hydrodynamics and control engineers have designed the hull, hydroplanes and control systems to provide control of depth and good manoeuvrability. The submarine must maintain neutral buoyancy and is literally ‘flown’ underwater.
PF: Have you single-handedly saved not only Barrow but UK submarine building as a whole?
ME: Absolutely not. Our success is about all 3,500 people in Barrow not one person. If an apprentice doesn’t turn up one day, it affects the whole team. It’s a team effort.
To use a football analogy if a team does well it’s not just down to the captain. Sure, you need a leader but you need all 11 players. It’s the same with us.
PF: How different would things have looked if you hadn’t turned round Astute?
ME: It’s my opinion that if things hadn’t changed, the MoD would have cancelled the Astute programme and there would be no submarines in the navy.
PF: Where does your work on Astute position BAE in terms of Trident?
ME: The government announced in March that the new Trident platform will be submarine based. It will be a new class of submarine, rather than an adaptation of the Astute Class.
We are the only people in the UK capable of building a submarine and a nuclear one at that. We have to be careful about complacency – they won’t come to us if we’re not cost effective. But yes, it’ll come here as long as we continue to be affordable.