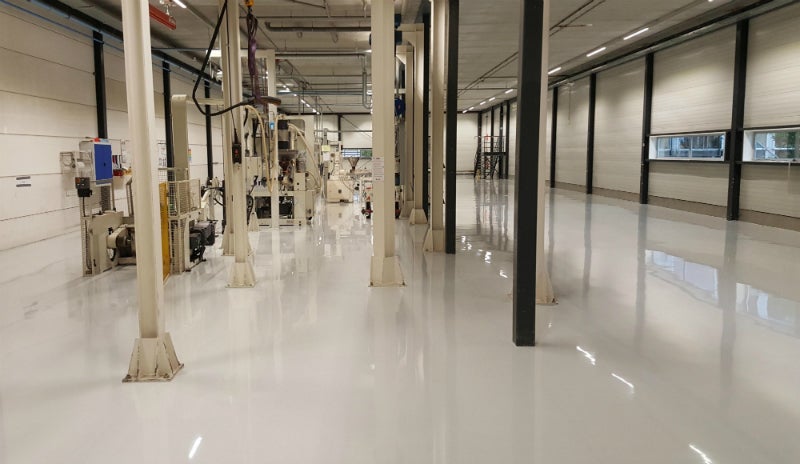
A stranded copper wire is used as the main component in our cables to conduct electricity.
Around it, we extrude a continuous layer of plastic to isolate the copper from its surrounding environment. Twisting this together with other components, forms our custom-designed cable.
The plastic has to be a good insulator and thick enough to prevent the copper from shorting to the outside world. Many of our cables operate in deepwater under high pressure, so we need to make sure that our insulation is sturdy enough to keep the water out. Plastic contamination causes insulation to deteriorate over time and eventually fail.
This year, we have been working on a new range of cables for ROV umbilicals, which control robots that operate at 2,000m to 4,000m underwater. In these types of extreme environments, minimising cable diameter is vital.
One way of achieving smaller cable diameters while retaining the same performance is to reduce insulation thickness. Further improving the cleanliness during manufacturing is then more important than ever. To do that, we looked at the room where the extrusion happens and have taken several steps to further minimise the risk of foreign material contaminating the cable insulation.
Firstly, we looked at the floor, which is made of reinforced concrete. Coating techniques have improved in recent years, allowing us to make a leap forward on our existing cleanliness. We opted for a coating with a triple-layer resin system. This has two major benefits. It eliminates dust rising from the floor itself and it highlights any dirt brought into the area that requires immediate cleaning.
We also invested in handling equipment such as pallet wagons with non-marking rubber wheels to keep the floor as clean as possible. Operators now wear shoe-covers to prevent any material from outside the extrusion room entering.
All doors now remain shut unless an operator enters or exits, and the air ventilation is configured to provide a slight increase in pressure so that whenever the doors open, the air will flow out rather than in.
We have taken the opportunity to upgrade the lighting system to LED lights. This gives us better illumination at lower energy cost while the light fixtures are much smaller, which reduces the surface areas where dust can gather.
We are now much more confident about the cleanliness of our plastic extrusion, allowing us to reduce insulation thicknesses without affecting quality.
Planning was a major challenge. All operations in the room had to be paused while deep cleaning was carried out and the refurbishment took place. The extrusion capability wasn’t available for a three-week period. Selecting the three-week block and bringing forward planned operations enabled us to keep promised delivery times under control.
The improved environment and increased lighting have a very positive effect on operator morale.