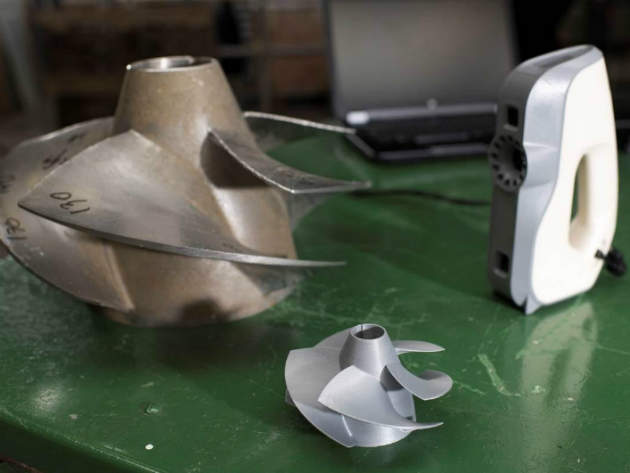
The Royal Netherlands Navy contracts work for the maintenance of its vessels and submarines to Dutch organisation Marinebedrijf Koninklijke Marine. In addition to maintaining the vessels, Marinebedrijf Koninklijke Marine is responsible for creating new parts for the ships to replace damaged parts, and carrying out modifications to on-board components when required, from everything to the hull to weapons systems and engines.
In order to speed up its servicing, Marinebedrijf Koninklijke Marine turned to Artec 3D, a company that produces 3D scanners that allow maintenance personnel to reverse engineer parts for vessels that need to be replaced, for which the drawings or 3D CAD files are not accessible.
The Artec Eva and Spider 3D handheld scanners used for this project are structured light scanners. The scanners work by projecting light in a grid pattern onto an object, which allows them to capture the deformation or distortion from multiple angles and then calculate the distance to specific points on the object using triangulation. These coordinates are used to produce a three-dimensional digital model.
Without 3D scanning, this reverse engineering process would involve a long series of tedious measurements for Marinebedrijf Koninklijke Marine.
“Using 3D scanning has saved us up to weeks of work – older processes were very intensive requiring multiple types of measuring tools and then replicating the drawing into a CAD programme,” says Ben Jansen, CNC coordinator at Marinebedrijf Koninklijke Marine. “Now, even when there is no 3D data or drawings of a part, we’re able to use an Artec 3D scanner to create a 3D image of the object, and the scan is used to reverse engineer the object. That part is then replicated using 3D printing techniques, 3-5 axis milling or 3D welding.
“In most cases, parts for the ships are being reverse engineered or newly created; this is especially the case in older navy vessels where the suppliers of the components no longer exist.”
Artec scanners
Since its first 3D scanner was introduced in 2008, Artec 3D’s technology has improved in accuracy and ease of use. The company’s current line-up full colour 3D scanners include the Space Spider, Artec Eva, Artec Eva Lite and the Artec Leo.
Artec Eva, which is best suited for scanning medium objects, has a capture speed of 16 frames per second. It captures and simultaneously processes up to two million points per second with up to 0.1mm accuracy. Artec Space Spider, which processes up to one million points per second and produces images of extremely high resolution (up to 0.1mm) and superior accuracy (up to 0.05mm), is best suited for small objects with intricate details. The Space Spider uses an advanced cooling system that allows it to operate at a constant temperature throughout the entire scanning process guaranteeing maximum accuracy.
The company’s newest scanner is the Artec Leo, an AI-based handheld 3D scanner that captures data at up to 80 frames per second. It can autonomously select and process data onboard, without connecting to a tablet or computer, allowing the user to watch while their object is digitized into a full colour 3D model in real time on the system’s multi-touch, half HD screen.
“Incorporating AI elements makes Artec Leo as user-friendly as possible,” Andrei Vakulenko, chief business development officer at Artec 3D, said. “Most scanners require somewhat tedious training in order to create professional scans, but the Artec Leo has broken down this barrier so that the process is intuitive and can be done by almost anyone.
“This will be what helps the 3D scanning market to grow, as it now can be utilised by a wider audience.”
Revolutionising support
Although it is still in the relatively early stages of adoption for military maintenance processes, 3D Artic is confident that its application has the potential to revolutionise the way military equipment is supported. Given the long service life of some platforms and the fact that even if full, up-to-date documentation on the equipment exists, it is likely to be restricted, making even small alterations to a platform can be a long, drawn-out and costly exercise.
“If you need to add anything to a military ship or plane – such as new seating or cupboards – the fastest and most accurate way to get the measurements would be to scan the areas,” Vakulenko said. “Quality control and inspection is another popular area, as parts such as propellers can be 3D scanned and checked regularly for quality assurance.
“3D scanning is also used for support; military ships are normally located quite far from their base, so in cases when technical support is needed, this is usually performed remotely. The area in question is often 3D scanned, so that the support engineer can better view the problem.”
Construction, control and crash testing
3D scanning can also play a role in supporting the building of new equipment.
“When you build any large object, be it a military plane or ship, the slight inaccuracies that occur during construction build up quite significantly, so the difference in the length of two ships of the same design could be several meters,” Vakulenko said. “So the only real way to know the exact size and shape of the ship would be to 3D scan it.”
3D scanners are an important tool for quality control here also – let’s say a part is machined using a 3D CAD file; the physical part can be 3D scanned to create a digital model. The digital model of the scanned part and the digital model used to create the part can then be compared to ensure that the component meets the required specifications.
Furthermore, 3D scanning is also commonly used for crash testing, both as part of a standard procedure to analyse the structure of an object and how to improve it so that it can better withstand a crash scenario, and in the case of real crashes so as to document what happened.
The 3D future
Further down the line, Artec 3D is looking to tap in to the move toward 3D printing and its application for military support on the move.
“When 3D printing takes off fully we expect that all large ships will have 3D scanners and 3D printers on board so that parts can be 3D scanned and then 3D printed on the spot,” Vakulenko said. “For large, sea-based vessels, this will really be an ideal solution – it will be far quicker than waiting for replacement parts to be sent from the repair base.
“At the moment, quite a few small parts can be 3D printed in durable plastic and used with great success, but the real breakthrough will come when 3D printers can achieve the same level of quality in metal.”