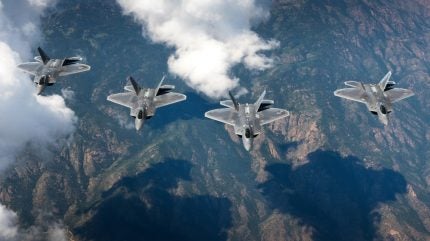
Advancing electronics has transformed the defense industry’s capability to gather and distribute information; foil, divert and track targets and scramble opposition communications within a networked spectrum. Electronic and “networked” warfare is a broad term that includes a variety of capabilities. These include the ability to “spoof” satellite systems that guide enemy missiles and drones as well as gain rapid access to intelligence from allies.
The war in Ukraine has brought to light Russian investment in electronic warfare technology, which is swiftly becoming the baseline for success in modern warfare. A lot is required from these sophisticated hi-tech components on the digital battlefield. Whether the mission-critical system is C5ISR, ISTAR, FADEC or ELMS, the basic requirements are dependability and high performance at a reasonable cost and in a small form factor.
After all, space, weight and power are at a premium on defense platforms. But guaranteeing the physical security of these powerful but physically delicate military communication systems, which must be resilient even when exposed to extreme temperature ranges, radiation, dust, and precipitation, is not straightforward.
Increasing energy density with confidence
For one thing, these complex networks of wires and microchips grow hot when running. The combination of more powerful processors, higher clock cycles, and greater board density all contribute to the need for more effective heat transfer.
Within harsh environments, fanless cooling is often required to shield sensitive electronics from air contaminants, reduced operating noise, and provide high levels of reliability. But in the past, the performance of conduction cooling was limited. Engineers had two options: limit the performance of their boards or opt for more expensive, less reliable, liquid cooled or heat pipe solutions.
The dilemma for the defense sector is how to regulate the internal temperature of electronics and protect them from the external environment without compromising performance or SWaP requirements. This is especially significant in airborne applications where weight equates to cost and in unmanned vehicles where the payload is the priority.
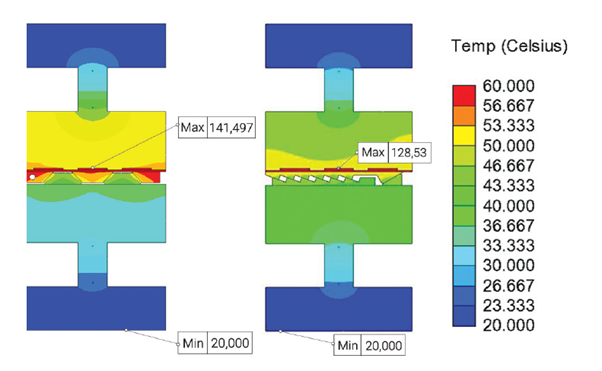
Additionally, the necessity of maintaining equipment in the field means that any upgrades have to be easy to use, repair, and replace. In field maintenance, repairs take place on the go, minimising costs while making equipment fully mission capable (FMC) more quickly. Products that are designed to be field maintenance compliant are therefore highly valued, but they need to be designed so they can be maintained and replaced by operators without specialised knowledge or tools.
To address these complex challenges, defense technology firm nVent SCHROFF has developed unique and compact new designs for card lock systems, which according to the company, are capable of providing the necessary protections to electronic equipment.
Better transfer of heat
“Higher clamp force equates to greater board retention and additional protection against shock and vibration,” says Matthew Tarney, aerospace and defense lead, who adds: “nVent SCHROFF’s Calmark High Clamp Force ‘HC’ Card Loks provide three times the clamp force of similarly sized Card Loks – up to 1250 lbs of clamping force depending on series. These figures are based on tests.”
nVent has also found a way to reliably cool and secure mission-critical electronics, enabling better thermal performance – by up to 15%.
“When two surfaces in contact have heat flowing across their junction, a measurable temperature difference arises caused by contact resistance. The value of this resistance is a complex combination of factors including surface finish, hardness, flatness, and contact area and pressure. In order to maximize the thermal flow, resistance must be minimized throughout the heat path,” says Gawtam Jhoty, nVent SCHROFF R&D engineer.
“The sawtooth design of our Card Lok is proven to decrease thermal resistance compared to a traditional similarly-sized Card Lok, which means it can then transfer more heat. The maximum temperature at the board is lower (128.5 degrees Celcius) versus the board installation with a traditional Card Lok installed (141 degrees Celcius). This means the HTS design facilitates a better transfer of heat away from the board.”
Let’s talk about Card Lok torques
For all Card Loks, obtaining the specified torque is critical for achieving optimal clamping and thermal performance. If the Card Lok is under-torqued, the clamping force may not provide enough retention, resulting in loose printed circuit boards and poor thermal transfer. If the Card Lok is over-torqued, the cold wall or printed circuit board could be damaged.
Attaining an accurate torque is typically done with a properly calibrated torque wrench, and usually requires some expertise as torque level varies by card lock design.
In rugged, high-stress environments, such as the battlefield, achieving optimal torque results can be immensely challenging. Conventional Card Lok must be actuated using a torque wrench, the torque wrench must be properly calibrated, and the Card Lok must be torqued to a specified level. In some situations, the operator may not have access to a properly calibrated torque wrench, specifically in cases where the operator’s tools are exposed to severe environmental conditions, or the operator may not know the proper torque level, which varies depending on the Card Lok design.
nVent SCHROFF’s torque-limiting Card Lok contains an integrated torquing mechanism that can be installed with any standard tool with a hex head, and when the correct torque is achieved, the mechanism ‘slips’ audibly to alert the operator. This simple but effective upgrade means operators can be assured electronics are secure even in the most dangerous environments.
Read more about nVent SCHROFF’s industry-leading enclosures for the high-tech military electronic systems on ships, tanks, ground control stations, aircraft and unmanned vehicles